Abstract
Highly reliable organizations in industries such as aviation and nuclear power serve as a model for how to improve patient safety and system performance in healthcare. This chapter explains the five basic principles of high-reliability organizations, with an emphasis on healthcare and radiology, and introduces tools and a framework that can be used to increase reliability and improve patient safety. The framework includes the three stage IHI model for designing reliable care systems, robust process improvement, and systems thinking. It also presents tools for increasing system reliability such as daily management systems, healthcare huddles, and the culpability decision tree.
Keywords
Healthcare quality, Healthcare redesign, High reliability, Just culture, Patient safety, Process improvement
Introduction
The Institute of Medicine’s reports, Crossing the Quality Chasm and To Err Is Human , created an awareness within the American healthcare system that change and redesign are necessary to improve patient safety and quality of care. This is exemplified by studies performed by RAND Health that found Americans with common health problems receive only 50% of recommended care. These needed changes clearly include healthcare professionals and organizations, but they also extend to the systems and processes within the healthcare environment. To address the inconsistencies seen in the delivery of high-quality healthcare, organizations have examined reliability principles from other industries such as nuclear power, the airline industry, and the military ( Fig. 8.1 ). Organizations in these industries must be highly reliable and perform highly predictable and effective operations in settings where hazards could result in harm to hundreds or thousands of people.
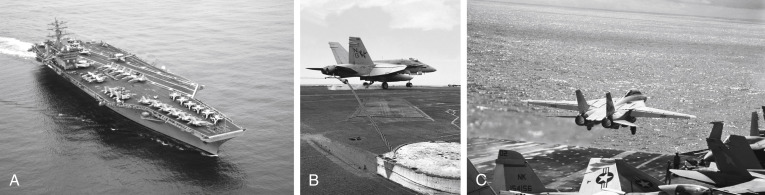
Reliability is defined as failure-free operation over time and is a measure of how consistently a system operates as intended. Reliability can be measured as the number of actions that achieve the intended result among the total number of actions taken. One can also measure the failure rate, which is calculated as 1 minus the reliability or the unreliability of a system. The unreliability of a system is frequently measured and is expressed as an order of magnitude where a system with a defect rate of one in 10, or 10%, performs at a level of 10 −1 . Studies suggest that the 10 −1 level is where most US healthcare organizations currently perform. This is far below the performance of the aviation and nuclear power industries, which perform at a defect rate of 10 −6 .
To move toward a high-reliability system, healthcare organizations, including radiology groups, need to adopt a culture of quality and safety. A culture is the attitudes, values, and behaviors of individuals when acting in a group or environment where they are encouraged to work proactively as a team. This culture should empower individuals to speak up and look beyond their own boundaries to ensure patient safety. Organizations should develop a shared vision with mutual accountability and frequent constructive communication centered around common principles of teamwork, especially when there are system failures. High-reliability systems must be flexible to respond to complex problems without error. This requires adherence to certain fundamental principles of high reliability.
Five Fundamental Principles of Highly Reliable Organizations/Systems
Weick and Sutcliffe devised five fundamental principles that are essential elements of all high-reliability organizations. Radiology groups and other healthcare organizations should work to incorporate these principles into their systems and practices to achieve higher levels of reliability. These principles include a preoccupation with failure, reluctance to oversimplify, sensitivity to operations, a commitment to resilience, and deference to local expertise.
Preoccupation With Failure
A preoccupation with failure is a proactive approach to prevent failures from occurring. In a high-reliability system, all employees at all levels are encouraged to think of ways in which work processes might break down or accidents occur. This shared mindfulness includes the full spectrum of failures, from small inefficiencies to catastrophic system failures, and allows for development of best practices within organizations. Errors that are detected are ideally corrected before any harm occurs, and employees are encouraged to report any near misses to further safe-proof systems and practices. It is important to destigmatize failure and see it as an opportunity for improvement. Evaluating and addressing the root causes of near misses throughout the chain of steps that lead to a potential failure are critical for increasing the reliability of a system. High-reliability organizations must also combat complacency with the status quo and embrace aggressive troubleshooting and continuous improvement.
Within radiology, the staff needs to be well prepared prior to beginning examinations or procedures. All necessary supplies should be readily available with extra supplies if necessary. Care providers should take ownership of their processes and actions and be prepared for potential complications. Radiology leadership should be committed to long-term process improvement and lead employees to see that success is attainable and borrow best practices from other successful operations within their department or others within the healthcare system.
Reluctance to Oversimplify
A reluctance to oversimplify is a principle of high-reliability organizations and systems that ensures problems and processes are deeply examined and appropriately managed. Although it is advantageous to simplify work processes whenever possible, high-reliability organizations see the risks inherent in a superficial approach. It is critical to respect the complexity of processes and problems and to explore problems deeply to find the root cause or true source of a problem so a meaningful solution can be formulated. Leaders of high-reliability organizations should constantly seek information that challenges their current beliefs as to why problems exist. They should also question explanations that may seem reasonable or obvious unless they are backed by data. This principle is applicable to radiology, which is a very complex field involving different types of imaging studies, techniques and protocols, acuity of examinations/procedures, reporting structures, and a wide range of diseases. A respect for these nuances is required when solving problems or redesigning radiologic systems or procedures.
Sensitivity to Operations
High-reliability organizations and systems are sensitive to their own operations and processes. Although it is common for organizations to have standard operating procedures, a highly reliable organization must be constantly aware of written procedures and policies and also what truly happens in the workplace. Certainly there is some level of disparity between what is official policy and what occurs in the real-time work environment, and highly reliable organizations are attune to this phenomenon. These discrepancies are both a potential occupational hazard and an opportunity for system improvement. In high-reliability systems, every employee needs to pay close attention to processes and operations to be aware of what is or is not working. This is particularly important in a field like radiology where there are numerous protocols and clinical scenarios that are routinely encountered.
Sensitivity to operations can be improved by increasing transparency, conducting leadership rounds, and using computer-generated analytics tools. Increasing intraorganizational transparency with improved communication and sharing of data regarding processes and problems engages employees and encourages them to pay closer attention. Hospitals or radiology groups might share patient safety or satisfaction data. Leaders in high-reliability organizations should also make workplace rounds to directly observe operations and have open communication with staff. Rounding improves leaders’ understanding of processes and allows an opportunity for staff to voice concerns or suggestions for improvement. Computer-generated analytics tools are also helpful in collecting process data and comparing documentation across multiple systems like the radiology information system (RIS), picture archiving and communication system (PACS), and electronic medical records. Analytics tools can be used to assist in regular internal auditing, which can uncover potentially dangerous discrepancies in process and sources of error. This should improve documentation, attention to detail, and process accuracy.
Commitment to Resilience
A commitment to resilience is a hallmark of highly reliable systems. High-reliability systems account for failures and are prepared to respond when they occur. Flexibility in a system is essential in mitigating failures and potential harm. According to Ashby’s law of requisite variety, a system must be more complex than its set of inputs to adapt appropriately to changes. Some level of redundancy should be built into a high-reliability system to provide flexibility during unexpected events or larger system failures. Radiology groups may have a backup physician or technologist available to cover for another’s unexpected absence. Radiology groups should develop a backup process when there are RIS or PACS failures for emergency interpretation and reporting. Large system redundancies are inefficient, but small redundancies are critical for resilience in times of failure. Highly reliable organizations are resilient and will bend without breaking when a large problem occurs.
Highly reliable organizations also see failures as critical learning opportunities. System failures occur within a matrix of processes and the causes are not always readily apparent. Once the immediate threats of a failure are neutralized, a longer-term analysis can begin. System failures are an opportunity to closely examine problems and processes to improve or replace them if necessary and increase future reliability. It is also important to evaluate how leadership responds to problems to drive future improvement and create a shared sense of resilience throughout an organization.
Deference to Local Expertise
Deference to local expertise is a fundamental principle of high reliability. It acknowledges that those in management and authority roles within an organization are not always the most experienced or knowledgeable. This is important when considering highly reliable performance in complex situations and settings. Although leaders will determine the overall organizational strategy for improvement, the frontline staff possesses vital knowledge about their work. Highly reliable systems encourage staff feedback and minimize the power distance between employees and management. For example, a first-year resident may have a more advanced degree and perceived rank than a senior ultrasound technologist; however, the experience of the technologist brings more value to the team. Deferring to the expertise of the most qualified individual regardless of title demonstrates respect, builds an environment of trust, and improves patient care. When working in healthcare and radiology, the vast and varying expertise of staff and complexity of clinical scenarios necessitates the empowerment of all staff members to improve care. Another important source of expertise is the prior work experience of all staff. Many healthcare workers have experience in other systems and leaders in high-reliability organizations encourage employees to share their prior experiences and incorporate foreign successful processes and systems whenever possible.
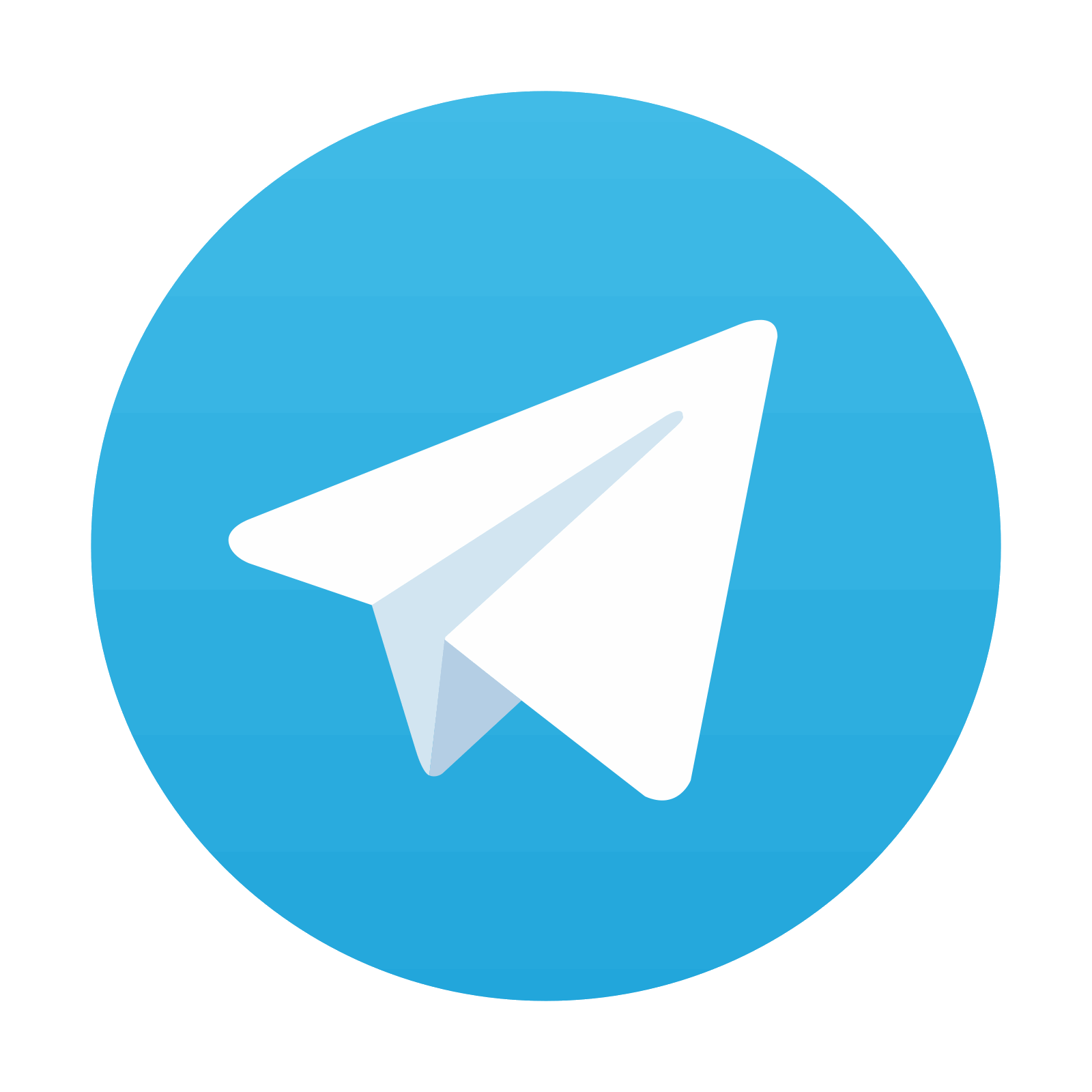
Stay updated, free articles. Join our Telegram channel
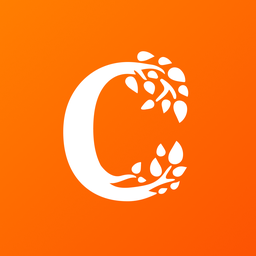
Full access? Get Clinical Tree
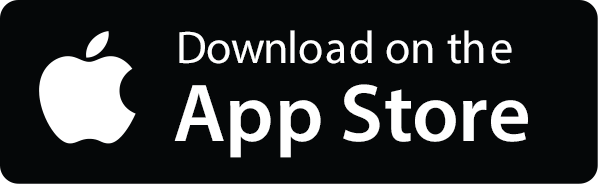
