Fig. 8.1
Gruentzig’s original coronary balloon angioplasty catheter. (a) First in man balloon made of polyvinyl chloride; (b) Double-lumen balloon catheter
Guidewires
Basic Construction
Guidewire technology has rapidly evolved since the early 1980s to meet the demands of complex coronary anatomy and pathology. As the severity and complexity of CAD increase, the need for more sophisticated devices also rises in concert. When designing guidewires, the following performance characteristics are vital:
(a)
Flexibility: the ability of the wire to bend when direct pressure is applied to the wire tip.
(b)
Trackability: the ability of the wire to be advanced around tortuous segments of a vessel and provide adequate support to deliver equipment around bends.
(c)
Torque transmission: a wire must be able to follow the course of the vessel. Torque transmission is the ability of the wire to transmit rotational forces to the distal tip of the wire in a 1:1 ratio to direct the wire into the desired vessel and maneuver around plaque or tortuous segment(s).
(d)
Support: the ability of the wire to deliver equipment (balloons, stents, atherectomy devices, intravascular ultrasound probe, etc.) particularly around vessel bends without the wire buckling. This characteristic is dependent on the core diameter and core material (discussed below).
(e)
Stiffness, including wire tip stiffness, is dependent primarily on the core material (steel vs. nitinol) and wire diameter.
Guidewires are made up of four components: (i) core, (ii) outer coating, (iii) the presence or absence of a polymer jacket or cover, and (iv) wire tip (Fig. 8.2).
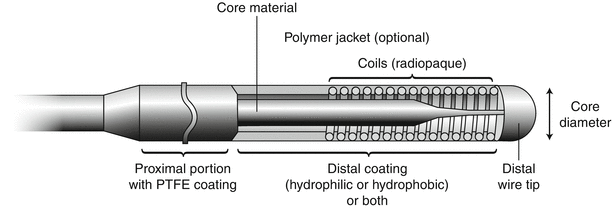
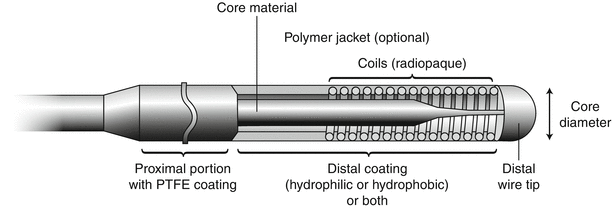
Fig. 8.2
Guidewire components. The proximal portion of most wires manufactured today are coated with polytetrafluoroethylene (PTFE), a hydrophobic material that provides a smooth, relatively frictionless surface across which balloons and stents can be passed with ease. The portion of the wire proximal to the PTFE-coated segment is composed of stainless steel
(i)
Core: The core of a coronary guidewire determines many of its performance characteristics. Core material is predominantly either stainless steel or nitinol or, more recently, a combination of the two. Stainless steel is a stiff material providing excellent support and has an enhanced ability to transmit push force and torque. Thus, historically, stainless steel wires have been used to deliver stents in more difficult-to-reach areas (i.e., calcified, tortuous segments). When employed in the wire tip, it allows easy shaping, though, stainless steel tends to unshape (“poor shape memory”). Nitinol (a nickel titanium metal alloy) was discovered in 1962 and became a core material of coronary guidewires in 1996. Nitinol possesses many favorable features as a core material. It has considerable flexibility, durability, and has excellent “shape memory” which is particularly important in the wire tip. Furthermore, it has the ability to resist both kinking and deformation. These characteristics make nitinol more difficult to form; however, once the desired shape has been achieved, its durability allows the wire to more likely maintain its shape for the duration of the procedure. Table 8.1 summarizes the key features of stainless steel versus nitinol. Since both materials have characteristics that are desirable in a guidewire, attempts have been made to design “hybrid” guidewires (e.g., Balanced Middleweight [BMW] family of wires, Abbot Vascular, RunthroughTM NS, Terumo Corporation), which provide the support of stainless steel and the flexibility and shape memory of nitinol. In such a construction, the wire core is composed of stainless steel “jointed” to a segment of nitinol using either an adhesive or is welded together. The BMW wire core, for example, is stainless steel proximally with the distal portion consisting of nitinol. The RunthroughTM NS wire has a nitinol core proximal end with the tip overlayed with platinum and stainless steel coils. An additional advantage to this hybrid construction is that such wires may be more reliably be used on more than 1 vessel in a single procedure due to its ability to maintain its shape and its ability to maintain a new shape if needed. Further developments in these two types of core material have resulted in variations within stainless steel and nitinol. As in any angioplasty guidewire, the core material possesses a certain degree of mechanical strength, which is best measured using a stress-strain curve (Fig. 8.3). With this in mind, developments have been made to improve the core material’s ability to withstand stress and resist deformation. For example, newer stainless steel wires often are “spring tempered,” which makes these wires more elastic, allowing them to withstand greater amounts of stress while still maintaining their original dimension. In other words, they are more resistant to damage during use. Likewise, certain nitinol wires possess super elastic properties that provide further resistance to kinking than conventional nitinol wires. Regardless of the material used, the wire core tapers towards the distal tip end (Fig. 8.2). If the guidewire core starts tapering more distally towards the tip, the coronary guidewire as a whole becomes more rigid providing increased support, steerability, and better torque transmission. However, with this design, there is a higher chance for wire prolapse. The opposite occurs when the core tapers more proximally allowing for a longer and more flexible tip (Fig. 8.4). An advantage of a more proximal taper is improved trackability of the wire. All coronary guidewires come in a range of overall diameters (0.010″–0.018″), the most common diameter being 0.014″.
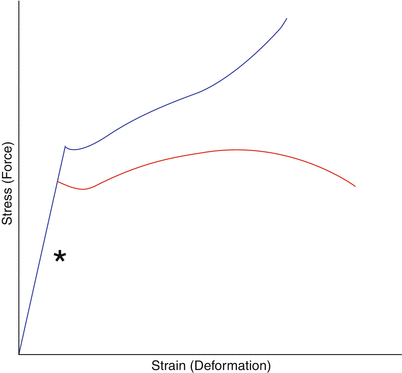

Table 8.1
Key features of nitinol and stainless steel as the core material
Nitinol | Stainless steel | |
---|---|---|
Rigidity/stiffness | Decreased | Increased |
Shape memory | Increased | Decreased |
Flexibility | Increased | Decreased |
Susceptibility to kinking | Decreased | Increased |
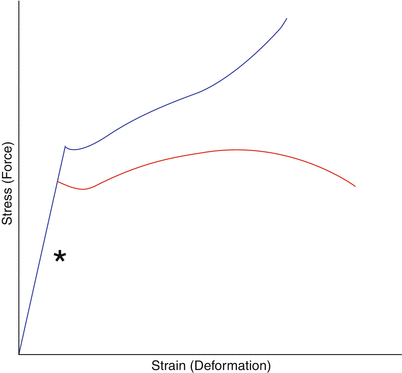
Fig. 8.3
Stress-strain curve of a guidewire. * denotes the elastic portion of the wire’s core material in which the material will return to its original dimension when the stress is relieved. The part of the curve beyond the linear portion denotes permanent deformation in which the material does not return to its original dimension even if the stress is relieved. The red curve is an example of a wire with non-spring-tempered stainless steel; the blue curve exemplifies a wire with spring-tempered stainless steel and demonstrates the increased elasticity seen with spring-tempered stainless steel

Fig. 8.4
Core taper lengths (long taper vs. short taper)
(ii)
Hydrophobic and hydrophilic coating: Guidewires are equipped with either a hydrophobic or hydrophilic coating for the majority of their length. Typically, guidewires have a hydrophobic polytetrafluoroethylene (PTFE, Teflon®) coat proximally and either a hydrophobic or hydrophilic coating in the distal 30 cm of the wire to provide lubricity and aide in the delivery of equipment. As one would expect, hydrophilic coats provide greater lubricity than hydrophobic coatings. Hydrophilic coatings typically consist of two compounds: polyethylene oxide (PEO) and polyvinylpyrrolidone (PVP). These hydrophilic compounds are used because of their biocompatibility and ability to reduce friction between wire and vessel wall in order to maneuver through areas of tortuosity and stenoses. However, the more hydrophilic a wire is, the less tactile feedback the wire provides the operator and the more likely the wire can enter the subintimal space. This is important when confronted with complex lesions where the operator may require better tactile cues. In contrast, hydrophobic coatings are silicone-based and are less lubricious than hydrophilic coatings. They provide improved tactile feedback and are more likely to stay in the true lumen and thus less likely to cause vessel perforations. Thus, there is a “tug-of-war” between lubricity and tactile feedback, wherein a wire may be more lubricious due to a hydrophilic coating ± polymer cover but will have less tactile feedback, compared to a wire with a hydrophobic coating (Fig. 8.5). There are, however, variations on the distal coating: some wires such as the Asahi Miracle Bros wires possess a hydrophilic coat distally with a hydrophobic coating at the most distal 1–2 cm of the wire. The rationale for this construction is to provide the lubricity of a hydrophilic coat while the most distal 1–2 cm of hydrophobic coating provides enhanced tactile feedback. In contrast, some wires do not have any coating on the distal tip, which theoretically provides additional tactile feedback. An example of this is the Balanced Middleweight (Abbott Vascular, CA), ACS Hi-Torque Floppy (Boston Scientific, MA), and Choice PT (Boston Scientific, MA). Finally, some wires contain a combination of hydrophilic and hydrophobic coat (examples include the Asahi Prowater and Confianza Pro 9 and Pro 12 [Abbott Vascular, CA]).
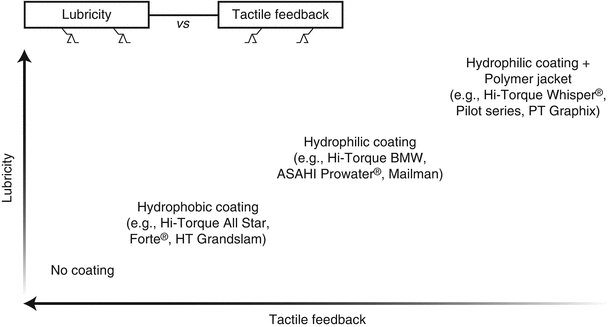
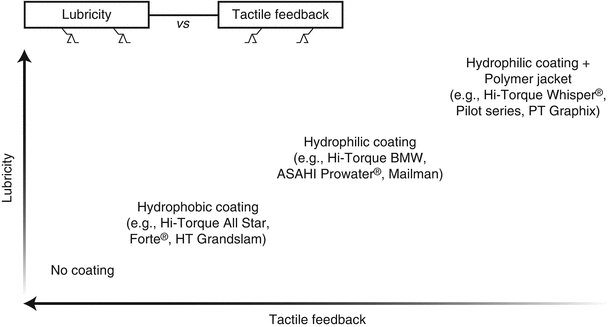
Fig. 8.5
Lubricity vs. tactile feedback
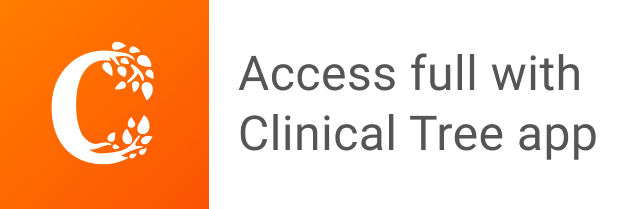